Material testing is a cornerstone of ensuring the safety, durability, and compliance of materials used in industries like aerospace, construction, automotive, and healthcare. As a lab manager or decision-maker, you understand the critical importance of operational efficiency and data accuracy in your lab. The complexity of handling diverse materials, instruments, and regulatory requirements demands streamlined operations and effective management.
In the United States, several materials testing labs stand out for their exceptional expertise and services. This blog highlights the leading materials testing laboratories in the US and examines how they manage operations, optimize their testing processes, and enhance productivity. For decision-makers in the field, these insights will offer a clearer view of how to manage lab equipment and software solutions effectively.
Top Material Testing Labs in the US
1. Laboratory Testing Inc. (LTI)
Located in Pennsylvania, Laboratory Testing Inc. (LTI) is a well-established provider of material testing and calibration services. They specialize in a wide range of tests, including mechanical testing, chemical analysis, non-destructive testing (NDT), and metallurgical evaluations. Their services cater to industries such as aerospace, defense, and manufacturing.
LTI faces operational challenges typical of high-volume labs—manual data entry and reliance on multiple systems for different testing services. These challenges can lead to inefficiencies, errors in data entry, and delays in report generation. Additionally, managing large quantities of data manually can create bottlenecks and hinder quick decision-making.
For LTI to maintain their reputation for speed and accuracy, optimizing workflows is critical. This could involve centralizing data into a single system to provide lab technicians and managers with faster access to test results, improve collaboration, and reduce errors. Additionally, automating repetitive tasks like data entry would free up technicians' time to focus on high-value tasks like testing and analysis.
ALSO READ | LIMS Integration: Benefits, Types, and Steps
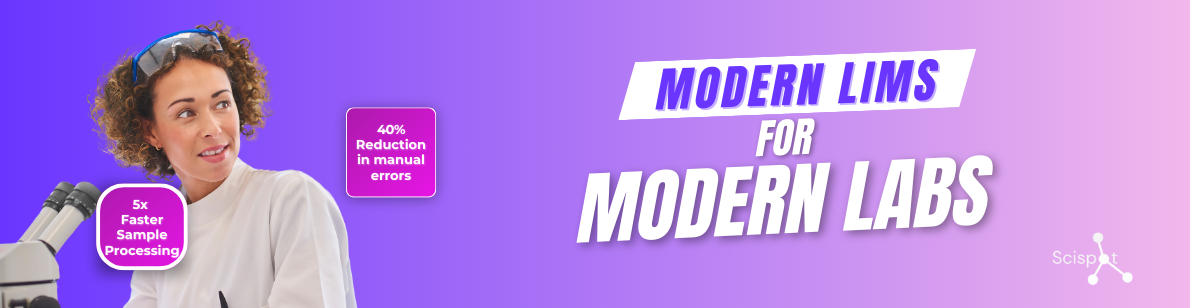
2. Element Materials Technology
Element Materials Technology is one of the largest independent material testing laboratories globally. Known for their services in tensile testing, fatigue testing, corrosion analysis, and environmental simulations, Element caters to industries including energy, transportation, and medical devices.
While Element's scope of services is impressive, one area where they could improve is data silos and the manual handling of reports. Multiple departments and systems often generate and store data separately, leading to inefficiencies when trying to access historical test results or compare data between projects.
To address these challenges, Element could focus on integrating their equipment with automated data collection systems, eliminating silos and manual errors. This would allow for faster access to test data and improved decision-making across departments. Furthermore, reducing manual processes would enhance operational flexibility, making it easier to scale up as demand increases.
3. Applied Technical Services (ATS)
For over five decades, Applied Technical Services (ATS) has offered mechanical testing, failure analysis, and metallurgical evaluations. ATS is recognized for their commitment to quality and customer service, serving industries like automotive, construction, and consumer products.
ATS faces challenges that many labs with decades of experience encounter—relying on multiple independent systems to manage different aspects of their testing services. This fragmentation often results in inefficient workflows and delays in report generation. Coordinating data across different systems can create bottlenecks, reducing efficiency in critical operations.
By implementing integrated lab management software that can consolidate data from multiple systems, ATS can streamline its operations. An automated system would ensure that data flows seamlessly between testing instruments and lab technicians, improving collaboration and efficiency. Moreover, streamlining the reporting process would allow ATS to provide clients with faster, more accurate results.
4. Lucideon
Lucideon is a global leader in advanced materials testing. They specialize in ceramics, metals, polymers, and composites and provide material optimization services for clients worldwide. Lucideon is known for its innovative approach to material performance testing and its commitment to ensuring compliance with the highest industry standards.
As Lucideon continues to grow, their challenge lies in data management, particularly when integrating new testing equipment with existing systems. The reliance on legacy data management systems can cause delays, especially when trying to compile and report results across departments. In an increasingly fast-paced industry, inefficiencies in this area can result in missed opportunities and slower time-to-market.
To address this, Lucideon could benefit from adopting a more unified system that can automate data entry and integrate with their instruments. This would eliminate the need for manual data handling, improving speed and accuracy while enabling them to manage increasing workloads effectively. With a more efficient data management system, Lucideon could better serve their clients with quicker results and more transparent processes.
5. Westpak
Westpak specializes in product and package testing, with an emphasis on mechanical and environmental evaluations. Their expertise serves industries such as pharmaceuticals, consumer goods, and electronics. With their focus on product safety, Westpak is known for providing accurate testing with quick turnaround times.
Westpak faces challenges with manual data collection and the report generation process. As a result, reporting can be slow and prone to human error. In industries like pharmaceuticals, where regulatory compliance is paramount, these delays could pose significant risks. Moreover, the inability to streamline test result data across multiple tests can lead to inefficiencies and a lack of real-time visibility into lab performance.
Westpak would benefit from automating key processes, especially data collection, sample tracking, and reporting workflows. By digitizing these aspects of their operation, Westpak could not only increase reporting speed but also reduce the risk of non-compliance in regulated industries. Additionally, automating these workflows would free up technicians to focus on higher-value tasks, such as test analysis and process optimization.
6. Metallurgical Engineering Services (MES)
With over 40 years of experience, Metallurgical Engineering Services (MES) is recognized for their expertise in metallurgical testing and failure analysis. They offer services such as microscopic examination, chemical composition analysis, and stress rupture testing.
Despite their expertise, MES still relies on manual systems for managing test data. This can slow down the testing process and create data fragmentation, as test results from different systems are not easily accessible in one place. As the demand for faster turnaround times increases, MES must modernize its data management process to stay competitive.
Implementing a centralized data management system would allow MES to automate data entry and streamline reporting. By eliminating the need for manual data handling, MES could achieve faster processing, enhance data accuracy, and improve overall operational efficiency.
ALSO READ |
7. RTI Laboratories
RTI Laboratories focuses on environmental and materials testing, specializing in surface analysis and corrosion testing. They serve industries such as energy production and transportation, providing advanced solutions to meet complex testing needs.
Although RTI Laboratories offers cutting-edge technologies, they face challenges with data integration. The reliance on separate systems for different instruments and tests often leads to inefficiencies and delays in generating test results. When managing complex data sets, it's essential for lab managers to have access to real-time information to make quick, informed decisions.
To optimize their workflows, RTI could benefit from integrating their testing instruments and data collection systems into a centralized platform. This would help eliminate bottlenecks, reduce manual intervention, and allow for faster reporting of results, enabling better responsiveness to client needs.
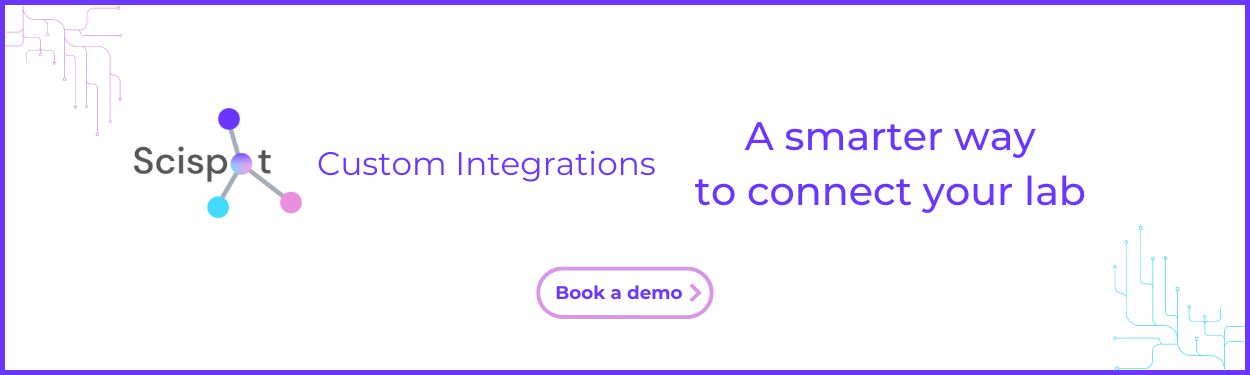
8. SGS North America
SGS is a global leader in inspection, verification, testing, and certification services. SGS North America offers an extensive range of materials testing services, including chemical testing, physical property testing, and environmental testing.
Despite its size and scale, SGS faces challenges with fragmented data systems that handle different stages of their testing processes. This creates inefficiencies and increases the potential for delays in delivering test results to clients. In the competitive world of materials testing, quick and accurate reporting is a crucial differentiator.
SGS could streamline its operations by integrating their testing systems and automating the reporting process. A more cohesive data system would allow SGS to reduce errors, improve communication between teams, and provide faster, more accurate results.
9. National Technical Systems (NTS)
National Technical Systems (NTS) offers a wide array of testing services, including shock and vibration testing, thermal analysis, and electromagnetic compatibility (EMC) testing. NTS serves critical sectors like aerospace, automotive, and telecommunications.
NTS struggles with manual processes for data management, which creates inefficiencies when managing large-scale testing projects. The need to track multiple variables and generate comprehensive reports quickly is essential, especially when working with highly sensitive data.
NTS could streamline their workflows by automating data collection and integrating testing systems into one cohesive platform. This would improve accuracy, speed, and efficiency, allowing NTS to meet tight deadlines and enhance their service offerings.
10. Intertek
Intertek is a leading provider of quality and safety services, specializing in materials testing, failure analysis, and performance testing for industries like electronics, automotive, and pharmaceuticals.
While Intertek is a global leader in materials testing, some regions still rely on manual data systems, leading to inefficiencies. These outdated practices can result in delays in report generation and difficulties in managing large datasets from various testing processes.
Adopting a centralized lab management system would help Intertek automate data entry, improve reporting accuracy, and ensure real-time access to test results. This would enhance the speed of operations, allowing Intertek to continue providing high-quality testing services across industries.
Why Material Testing LIMS Is Important
Material testing labs operate under high pressure to deliver fast, accurate, and compliant results. A Laboratory Information Management System (LIMS) is crucial for automating workflows, managing sample data, and ensuring regulatory compliance. A LIMS system like Scispot enables labs to manage large volumes of data while minimizing human error and delays.
Without a LIMS system, labs risk facing operational bottlenecks, delays in reporting, and compliance issues. In a world where safety and compliance are paramount, failing to track data effectively can result in product recalls, regulatory fines, or worse—unsafe materials reaching the market.
Imagine the Consequences: Without a LIMS system, a small data entry error can snowball into costly mistakes. Delayed reports could impact time-sensitive decisions, resulting in financial losses or a tarnished reputation. Moreover, when labs fail to meet compliance standards, they expose themselves to legal repercussions and loss of client trust. Is that a risk your lab is willing to take?
How Scispot alt-LIMS Helps Material Testing Labs
Scispot offers a tailored LIMS solution designed to meet the unique needs of material testing labs. By integrating data, automating workflows, and ensuring compliance, Scispot empowers labs to operate efficiently and competitively.
Integrated Data Management
Scispot connects instruments into a single platform, enabling seamless data collection and analysis. This reduces retrieval time, enhances accuracy, and eliminates silos, ensuring lab managers have instant access to critical insights.
Automation
From sample tracking to report generation, Scispot automates repetitive tasks. Labs can process higher volumes with fewer errors, cutting turnaround times and allowing technicians to focus on analysis rather than paperwork.
Compliance Assurance
With built-in tools for audit-ready workflows, Scispot ensures adherence to standards like ISO 17025 and ASTM. This minimizes compliance risks and simplifies regulatory reporting.
Real-Time Analytics
Scispot provides real-time insights into sample throughput, report times, and lab performance, enabling data-driven decisions and operational improvements.
Collaboration Tools
By linking data and workflow management, Scispot fosters seamless teamwork, improving communication and productivity across departments.
Book a Demo
Ready to transform your lab operations? Book a demo today and discover how a LIMS solution can help your material testing lab achieve higher efficiency, improved data accuracy, and greater compliance with industry standards.
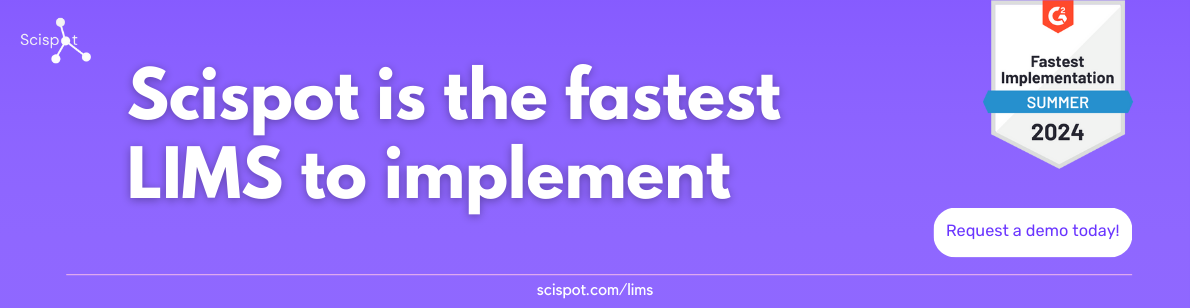